Explore the
Nation's First
aTULC CAN PLANT
Discover the forefront of packaging sustainability and beverage innovation at American Canning's aTULC can plant. Step inside our facility to witness how unique liner technology, prioritizes environmental responsibility while redefining industry standards.
.png)
.png)
.png)
.png)
.jpg)
.png)
.png)
.png)
.png)
.jpg)
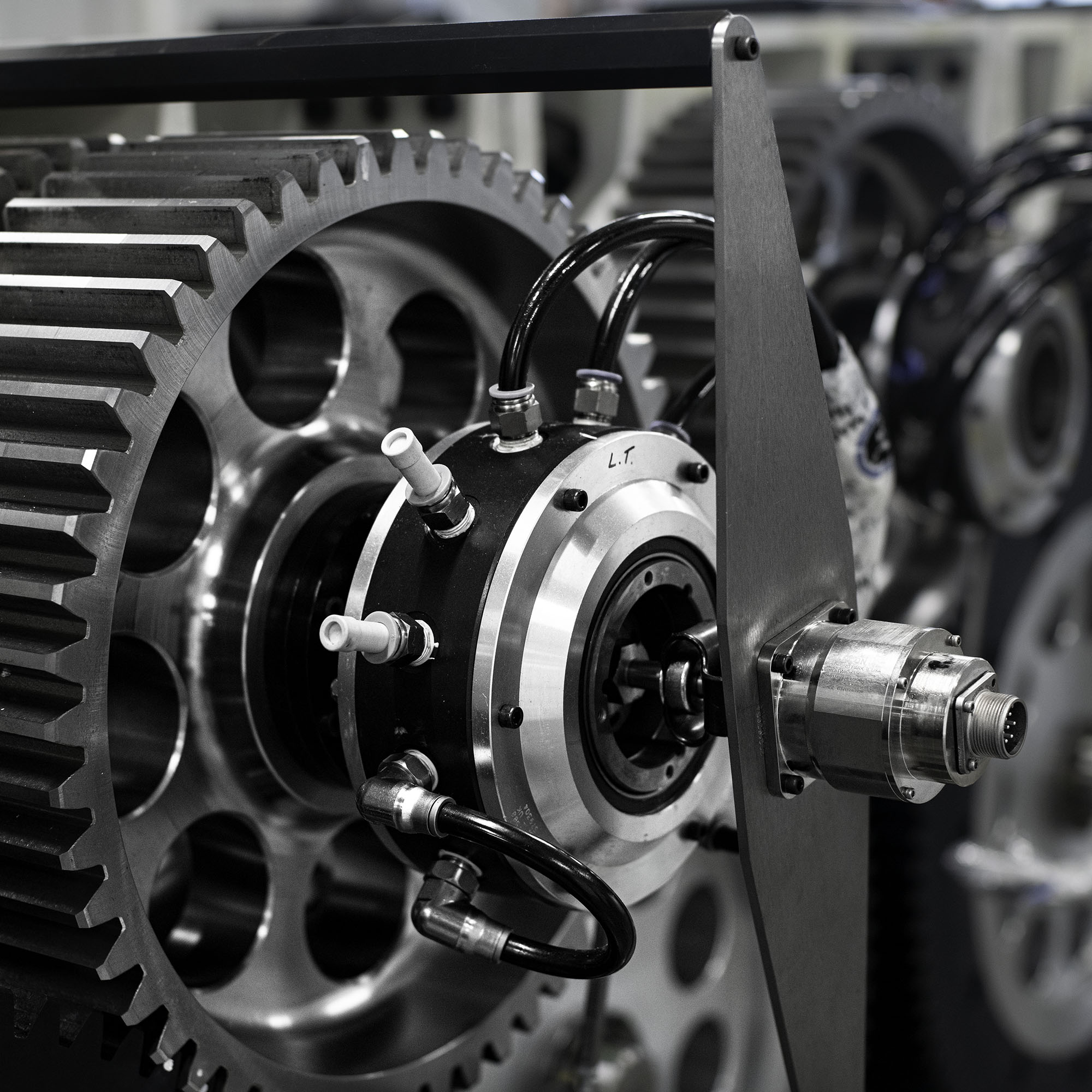
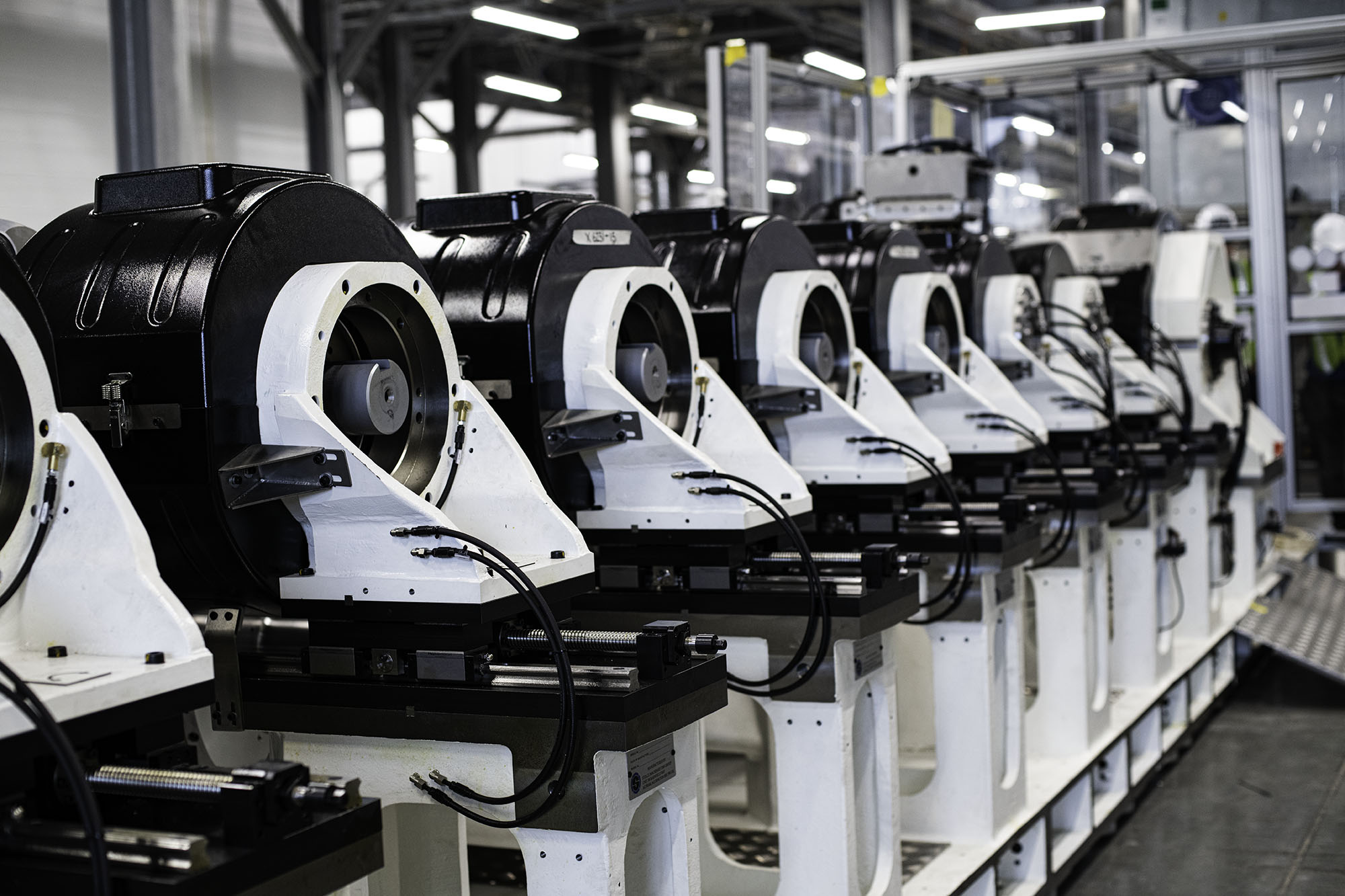
.png)
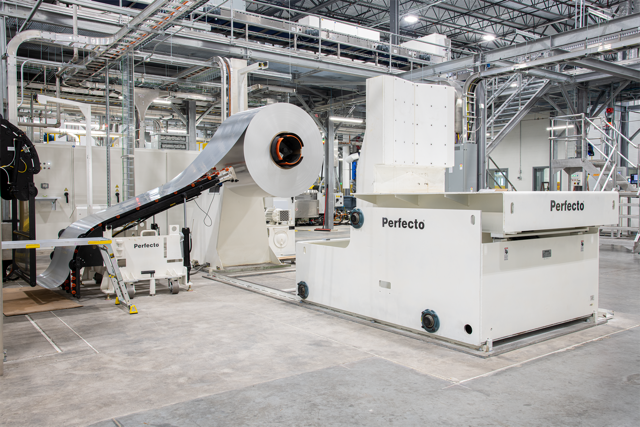
.jpg)
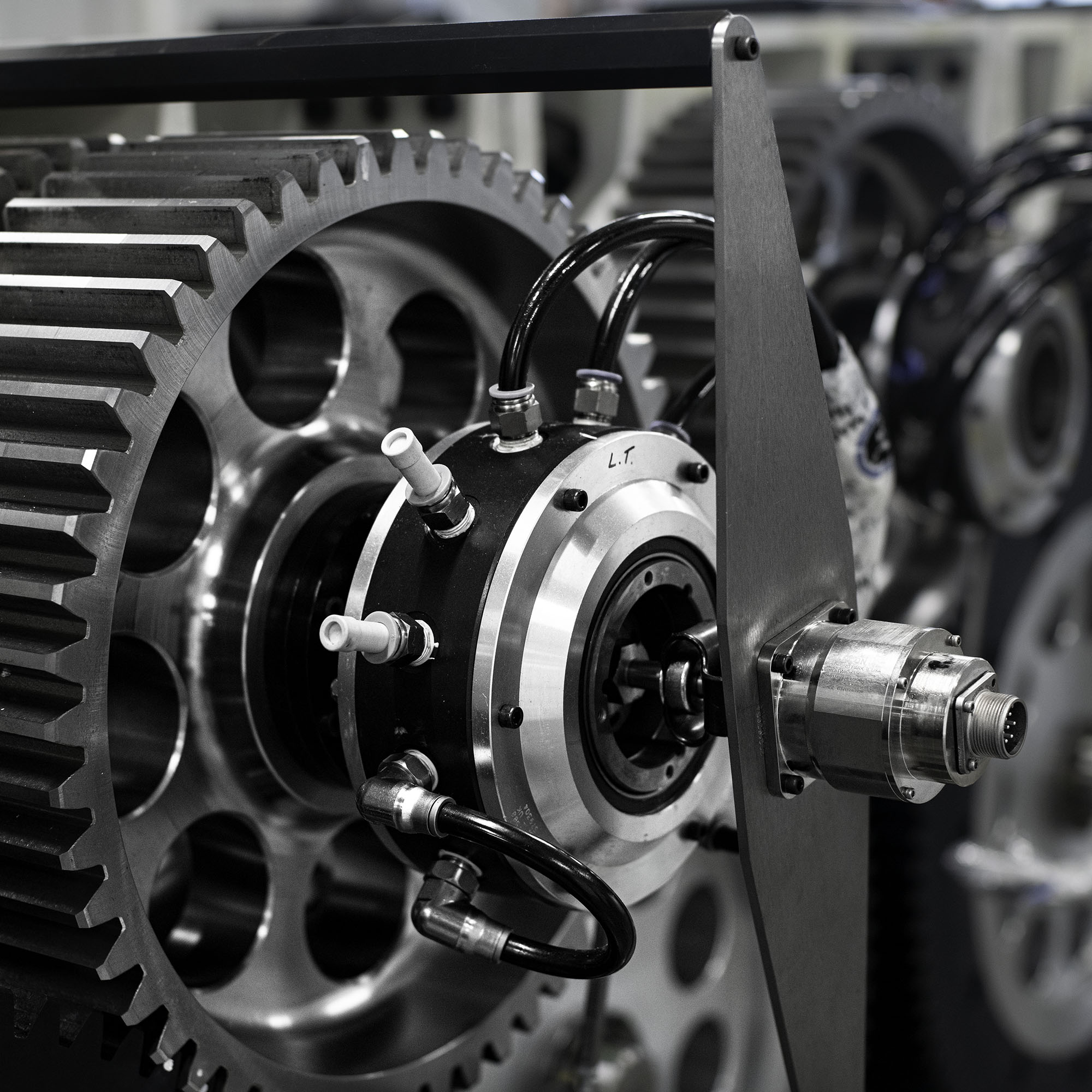
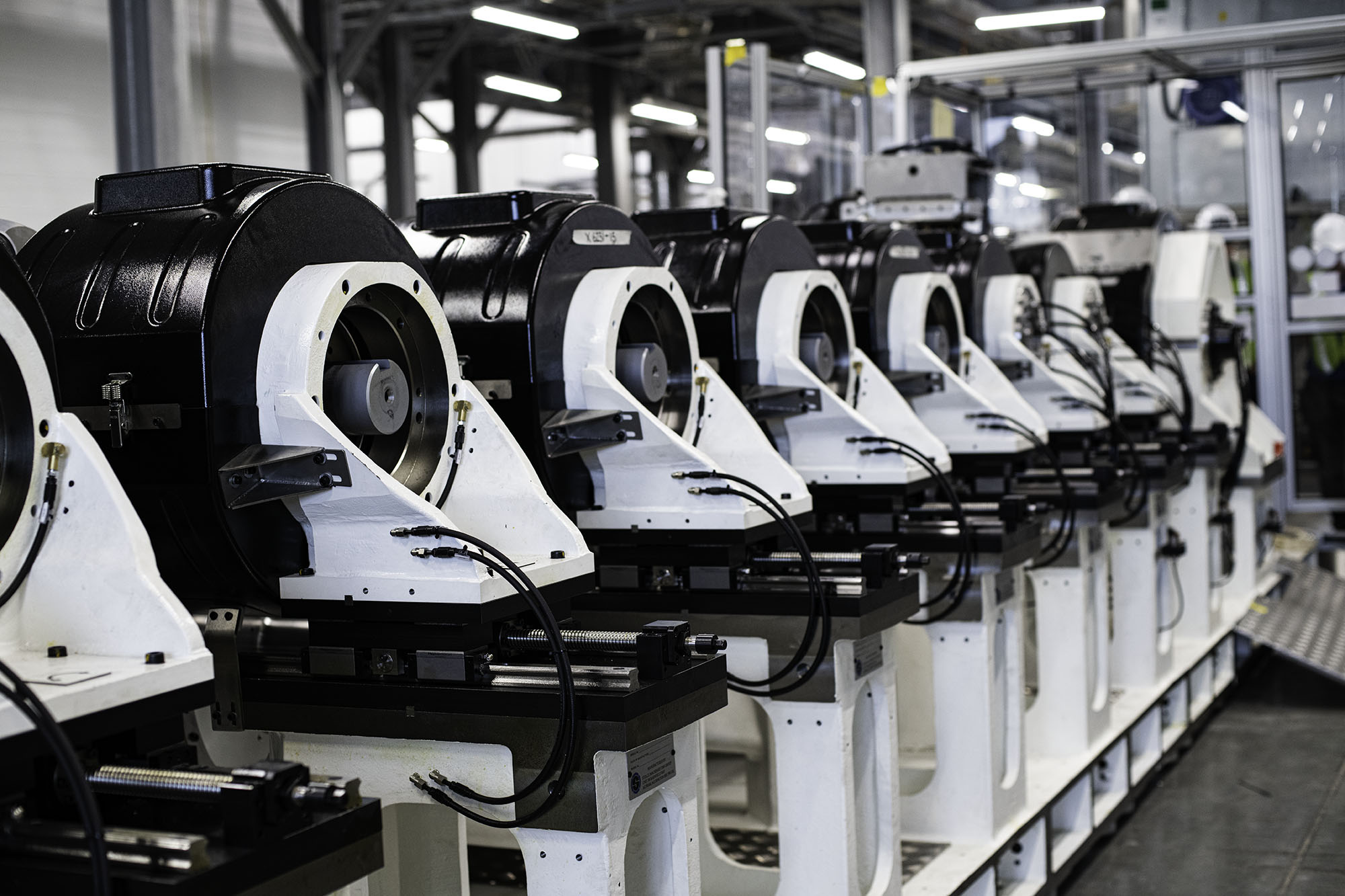
.png)
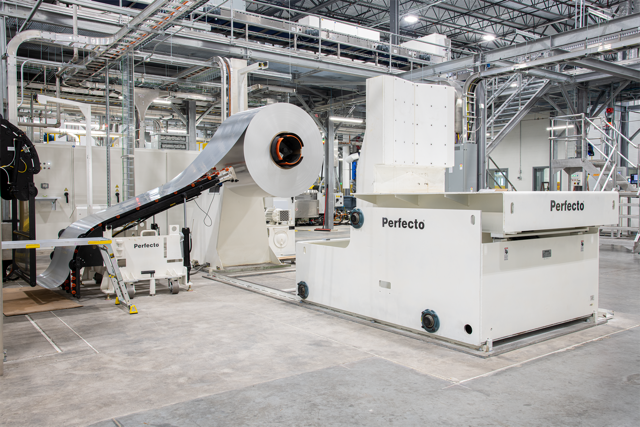
.jpg)
A MORE SUSTAINBLE WAY TO MAKE CANS
aTULC technology was created to offer more sustainable packaging. It aims to reduce material and energy consumption during production while maintaining superior can durability.
form and line the cans.
our plant saves 20,000 gallons of water per day.
The Significance of aTULC Now Being in the US
The establishment of a US-based aTULC manufacturing facility plays a crucial role in supporting premium beverage and beverage innovation throughout the United States.
By localizing production, American Canning ensures a more reliable supply chain and faster turnaround times for producers needing to respond quickly to market demands, and requiring a more durable, high performance beverage can.
The commitment to sustainable manufacturing practices reflects a shared value, not only with producers, but with end consumers who prioritize environmental responsibility.
This alignment not only fosters growth within the beverage industry but also strengthens community and economic development by supporting green jobs and technologies.
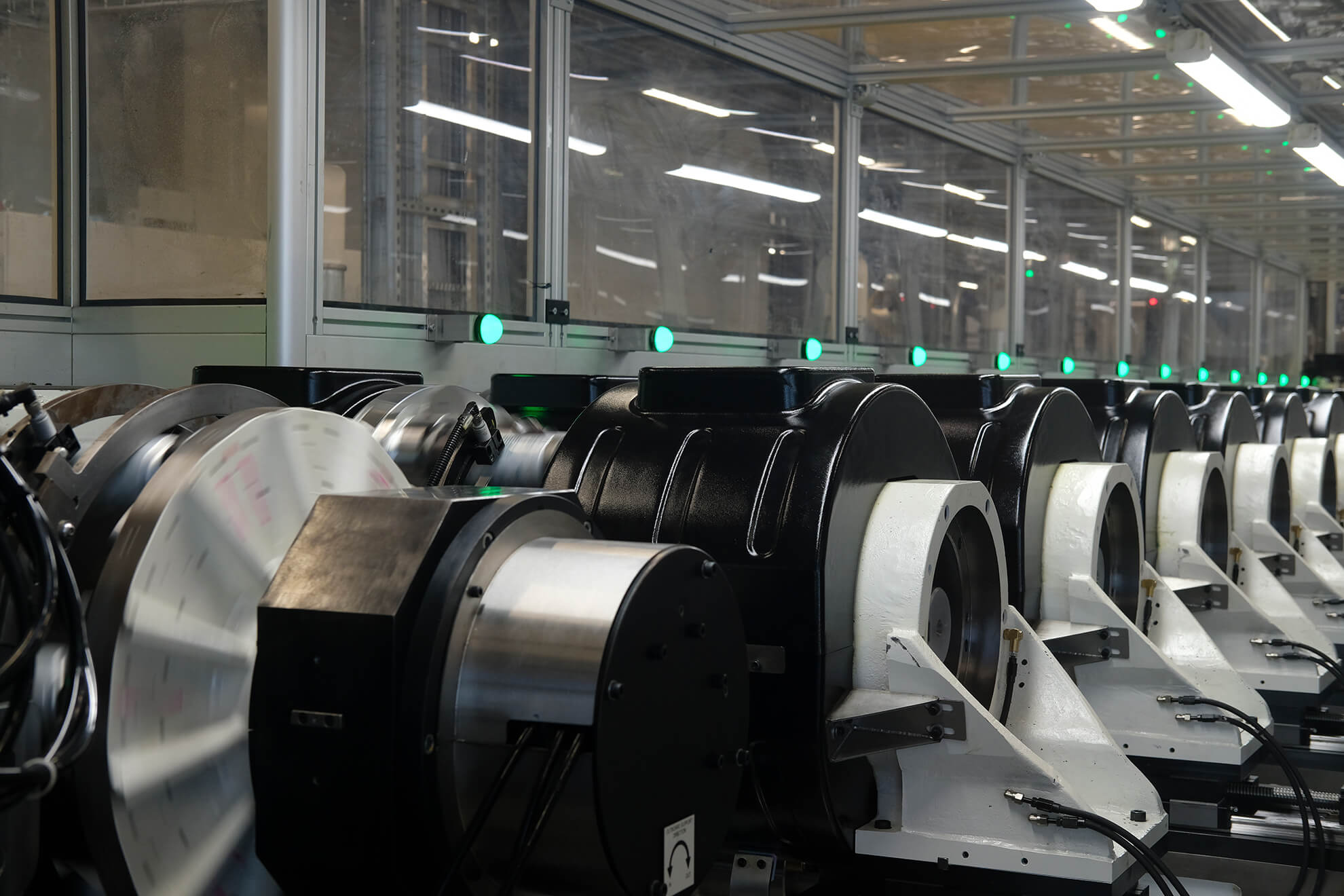
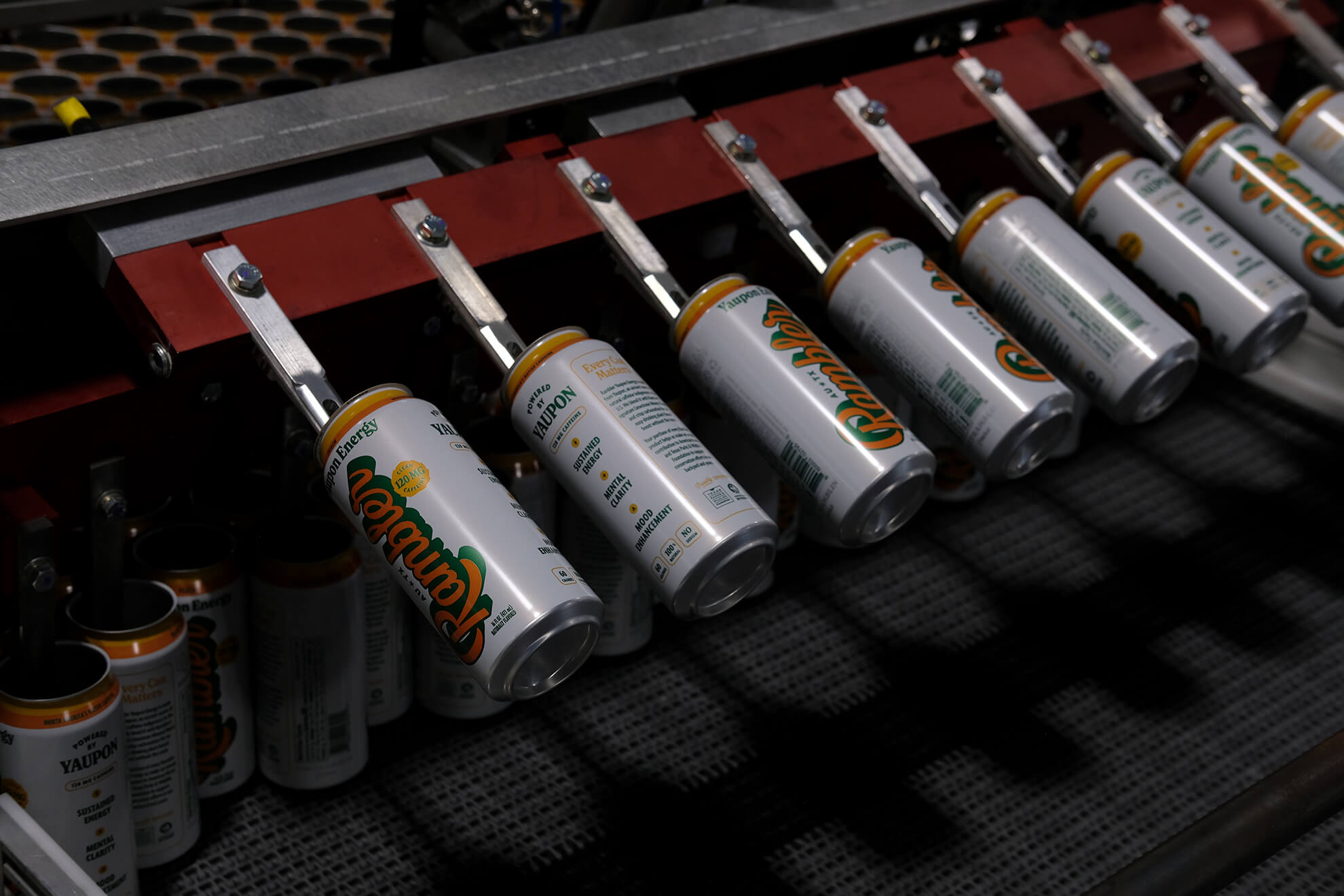
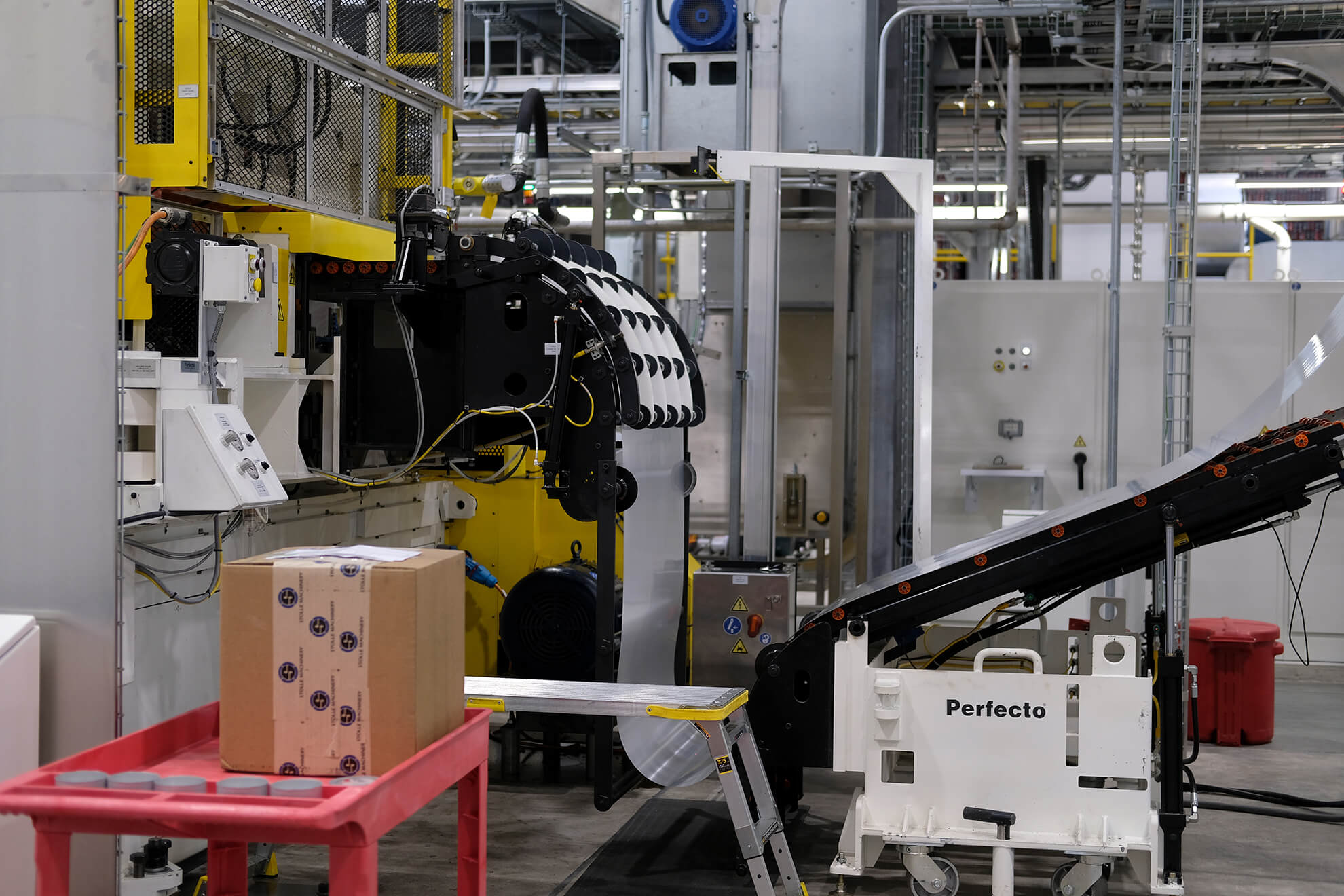
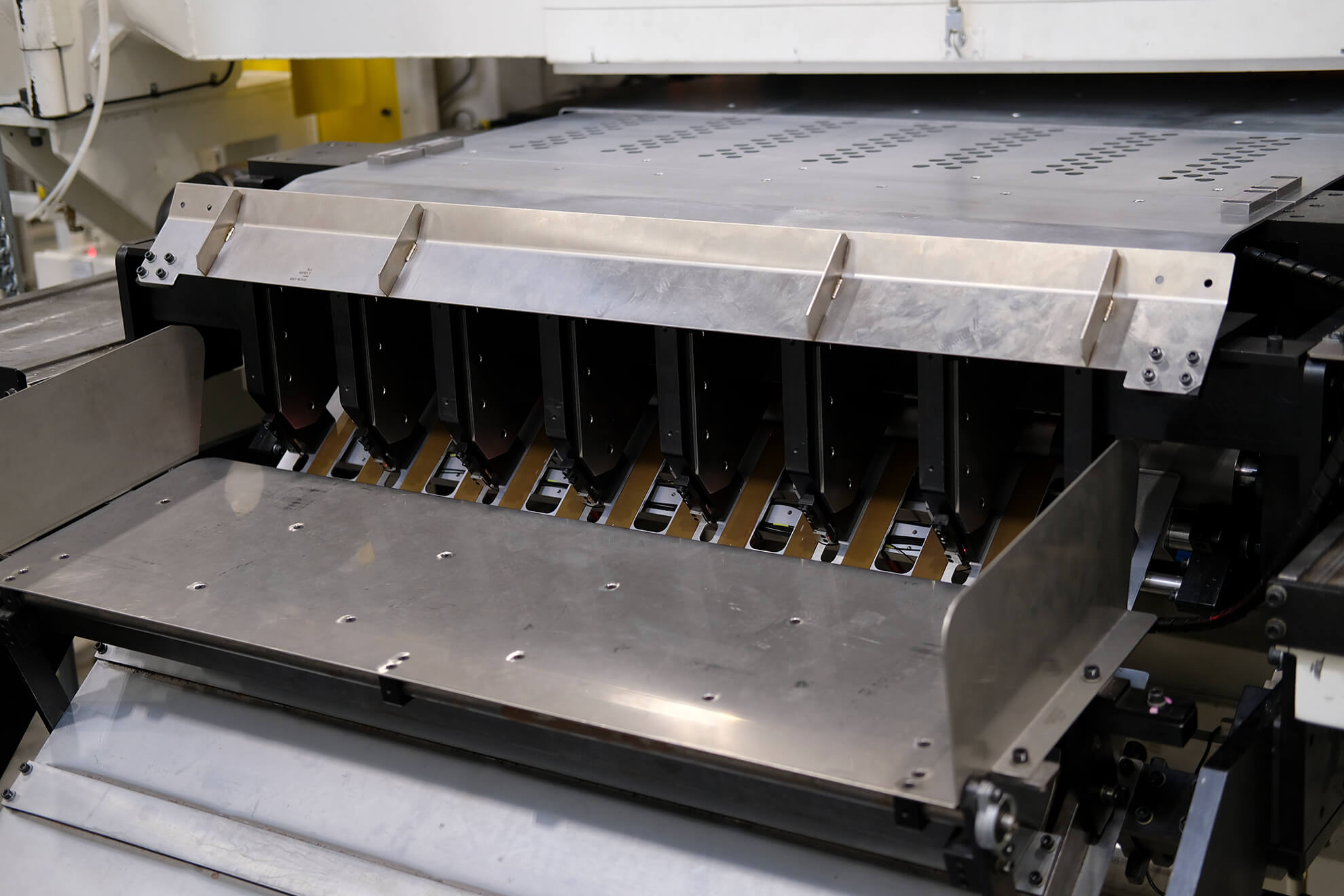
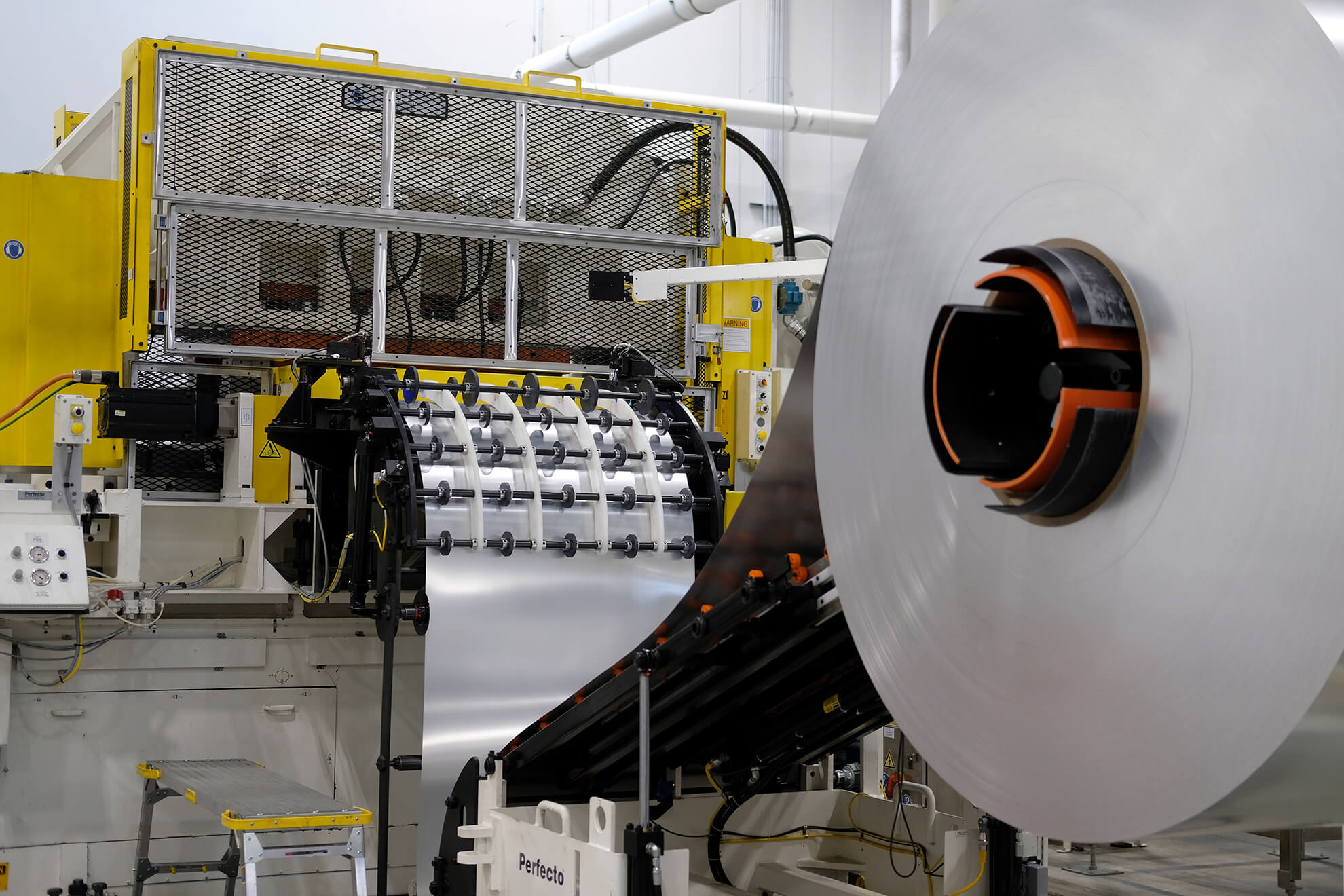
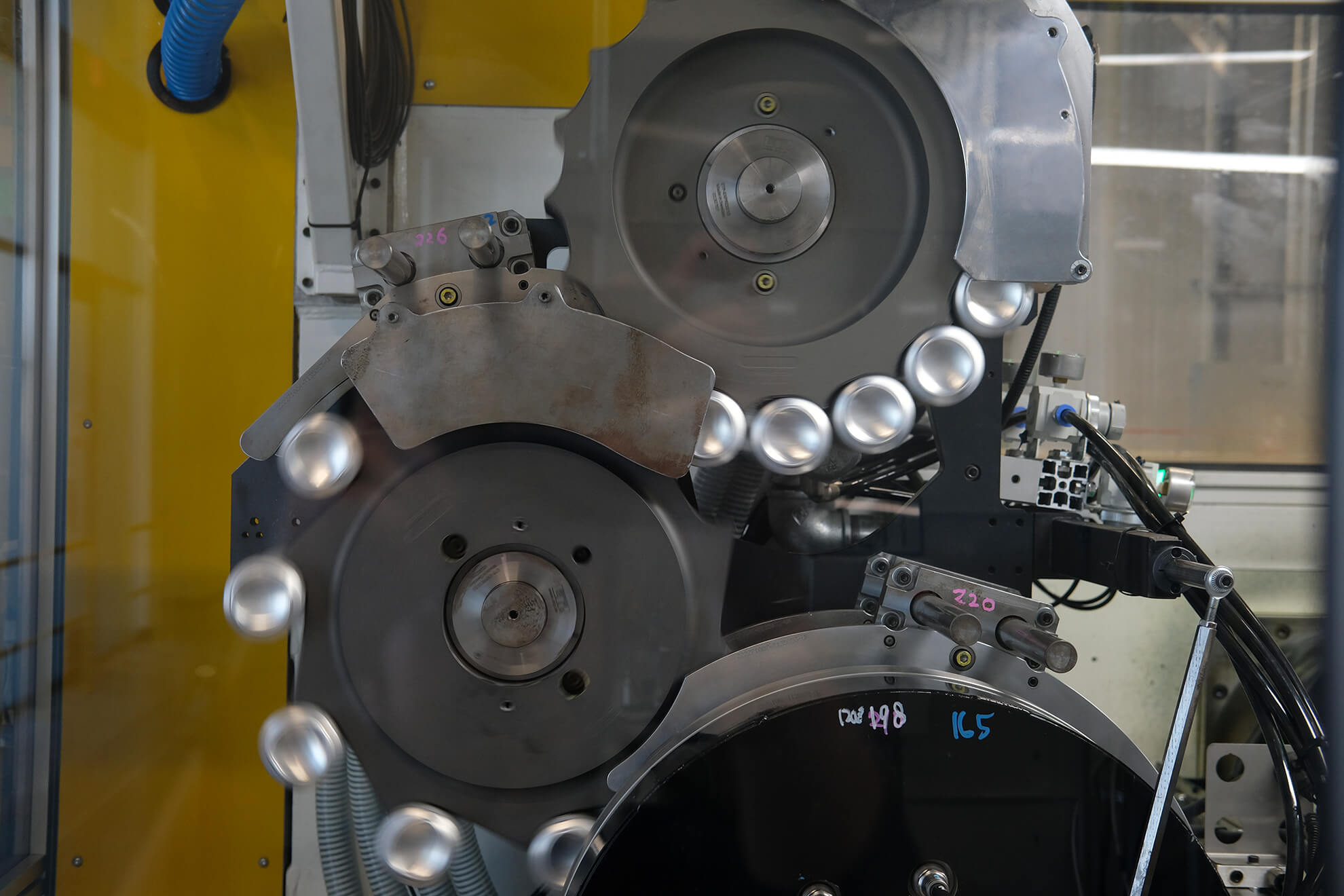
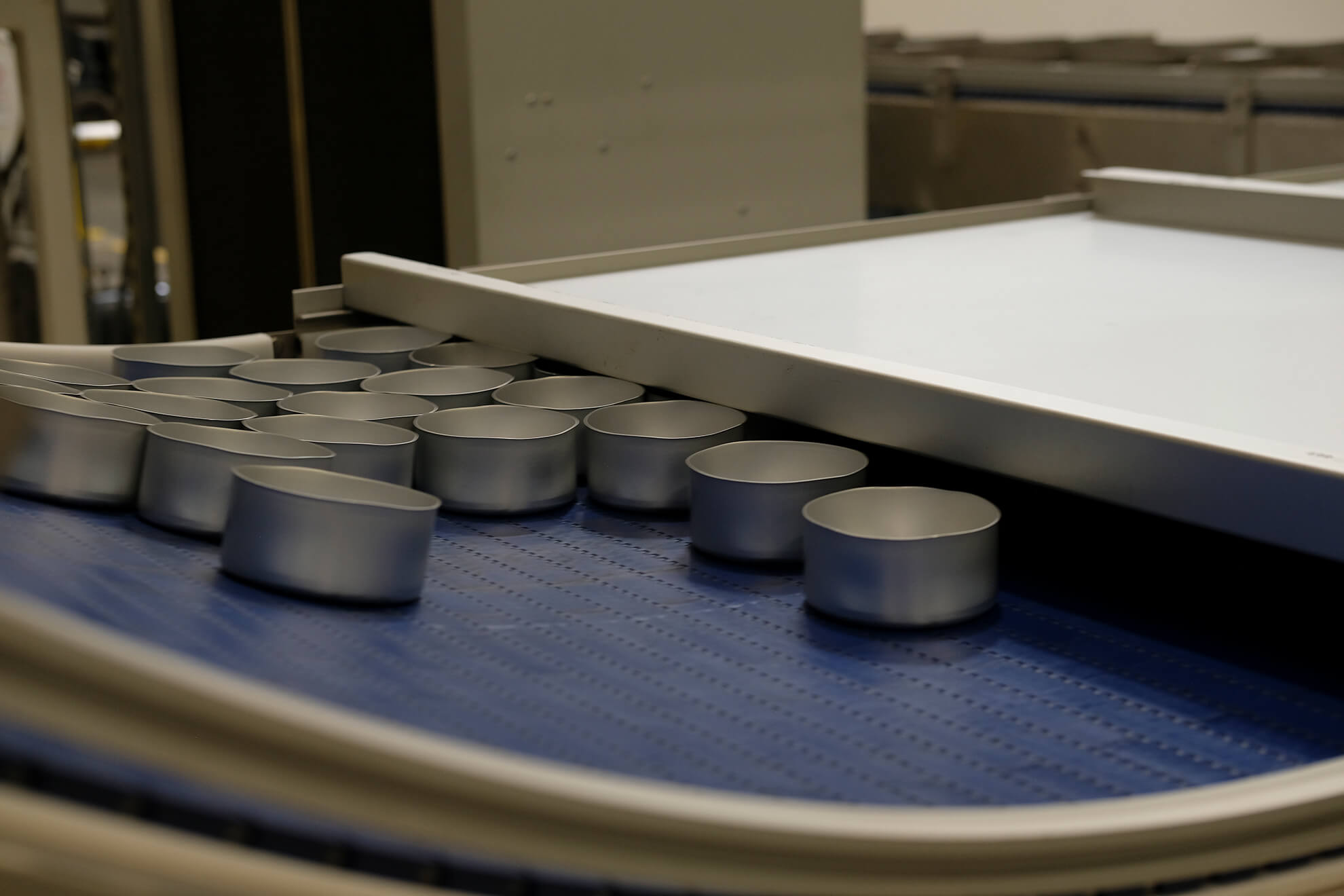
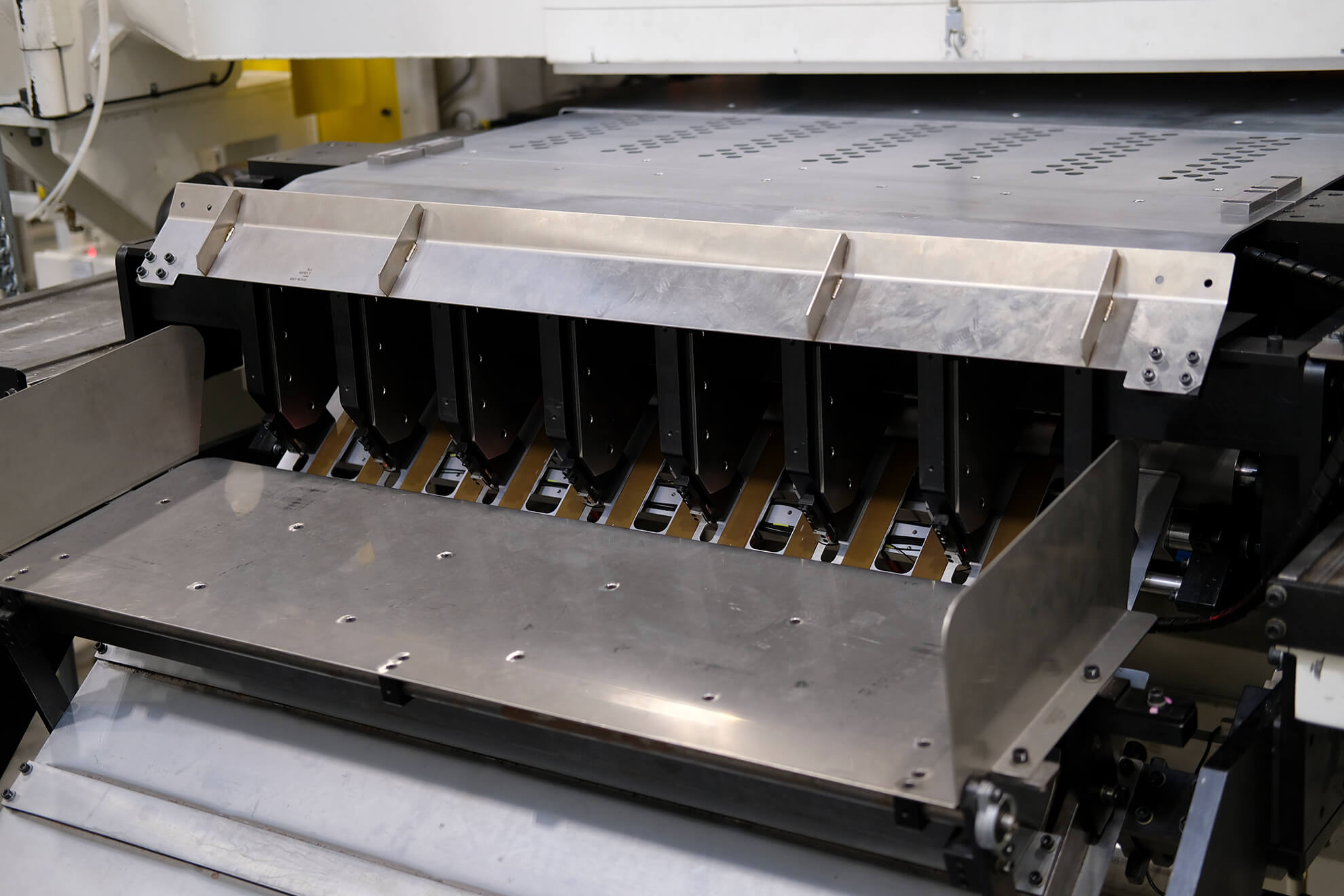
maNufacturing that matters
Infinite recyclability
aTULC CANS ARE infinitely recyclable.
RESOURCE SAVINGS
in the production of aTULC cans.
GREEN, URBAN Jobs
Green Manufacturing jobs in austin.
HOW IT'S MADE
Up-Ender & Un-Coiler
Aluminum enters the can plant as large, rolled coils. The up-ender turns the coil to position and transfer it to the un-coiler where the aluminum sheet is rolled out and fed into the cupping press.
Fun Fact:
- 1 roll of coil will produce ~430,000 cans
Cupping Press
As coil is unrolled and fed through the cupping press, two operations are performed
- The machine punches out a disc
- The disc is drawn into a shallow cup
The webbing, or remainder of the cut-out material, is cut into pieces and sent through a vacuum system to be compacted with other scrap material that is then recycled.
Fun Fact:
- 8 cups are punched per stroke
- There are up to 130 strokes per minute
Body Makers & Trimmers
At the body makers, cups are drawn and ironed into the body of a can.
The coating on the aluminum sheet acts as a lubricant during this process, negating the need for lubricants and further processing typically be seen in traditional can plants.
When formed, the can bodies have an imperfect edge and taller walls than required. Excess material is cut off via trimmers leaving the can the exact height with a perfectly straight edge. Trimmings are sent through same system as the webbing from the cupping press to be recycled.
Fun Facts:
- Each body maker runs at 300 strokes per minute
Heat Set Oven
Trimmed, straight-wall cans are conveyed to the heat set oven, which relieves stress that is induced in the aluminum coating caused by the forming process. This process ensures that the integrity of the liner is upheld.
Fun Fact:
- It takes 14 minutes for an aluminum can to be made.
Decorator
Following the oven, cans are ready to be decorated via a dry-offset process. The decorator includes printing plate cylinders, blankets, and inkers.
There are 8 inkers which apply ink to a printing plate cylinder that then transfers each color onto a blanket until the entire design is picked up. The blanket acts as a stamp, transferring the design onto the can in a single pass. To complete the decoration, a layer of over-varnish is applied to protect the ink and give the can the desired glossy or matte finish.
Fun Facts:
- Inks are hand-mixed
- The process repeats 1000+ times per minute
Can Transfer & Outside Bake Oven
Coming out of the decorator, ink on the cans is wet/sticky.
The can transfer system moves cans from the decorator to the outside bake oven. Cans are evenly spaced and travel through a 400F oven which cures the ink and varnish on the exterior of the cans.
Spacing and speed are important to ensure complete and even heating, keeping wet cans keep from touching one another and smearing designs, or sticking together.
Fun Fact:
- It takes 3 minutes for cans to pass though the oven
Necker
The necker is the final forming stage, taking can bodies from a straight wall cylinder to a fully-shaped, ready to fill can.
The neck is formed across 12 stages with the final step creating a curved edge (flange) so a can is able to be seamed.
A series of quality checks are performed at this stage:
- A light tester checks for pinholes
- Metal Exposure Testing (MET) detects liner defects
- A vision system inspects four regions of the can for physical defects, automatically rejecting defective cans
Fun Fact:
- 100% of aTULC cans go through MET testing
Palletizer
Cans are nested into a pattern of 389 cans per layer and swept onto a pallet one layer at a time until the desired number of layers are accumulated.
Once complete, a top frame is placed on the pallet and tightly banded.
Pallet of cans are now ready to be shipped to production facilities to be filled with beverages for everyone to enjoy!
Fun Fact:
- 12oz can pallets are stacked 21 layers high
- 16oz can pallets are stacked 16 layers high